
Energy Audit
Energy audit is the easiest way to achieve higher profitability in a manufacturing setup. Industrial energy audit carried out by B.E.E. Certified Energy Auditors can yield results for any type of manufacturing plant in terms of electrical energy saving and fuel saving. Typically a plant can save a minimum of 5% energy through our energy audit services. Energy audit should be a voluntary exercise as it saves production or manufacturing costs and has a direct impact on profitability. It is mandatory for energy-intensive industries to carry out a periodic energy audit and some States like Gujarat have also mandated Gujarat Electrical Inspector Energy Audit. Whereas the Central Government has mandated frequent energy audit for energy intensive industries such as steel, cement, aluminum etc.
Energy is one of the easiest controllable cost components in manufacturing yet it is the most neglected in many cases. Manufacturers can actually improve their profitability by optimizing their energy usage through energy conservation and energy efficiency.
Energy conservation is an ongoing process as new systems develop and equipment ageing take place. While several plants do put energy conservation measures in place an energy audit by certified experts helps in fast-tracking the progress towards energy efficient operations.
In a manufacturing setup, energy can be saved through
-
Plugging leakages in the existing systems (energy saving)
-
Optimization of technical processes (energy efficiency)
-
Use of advanced technology retrofits (system efficiency)
-
Optimization of non-technical processes (process efficiency)
-
Replacement of old systems by new-age systems (system efficiency)
As per IEA (International Energy Agency) end-use energy efficiency can result in maximum mitigation of Green House Gases (GHG). It estimates that end-use fuel and electricity efficiency would be responsible for 34% of total mitigation. Whereas renewable would be responsible for 17%. So energy conservation and energy efficiency is not just beneficial in terms of cost-saving but it also helps in sustainability.

Energy savings can be in the form of direct saving of fuel being used in process or electrical power. It also leads to saving of derived energy such as steam, compressed air, hot water etc. the savings of which result in saving of manufacturing costs.
(Aluminum smelter energy audit case-study : Available on request. Drop a mail to info@EnercoEnergySolutions.com or Enerco@Ymail.com)
Energy Audit by a competent team led by B.E.E. Certified Experts can help a plant save at least 5% on Energy bills. This can have immense benefit for manufacturers who wish to cut down on their cost of production. Combined with data-driven intelligent automation can help a manufacturer save significant amount and directly impact their bottom-line. We did carry out an IIoT study for a steel manufacturer. See our Industry 4.0 IIoT case-study to understand the savings.
Our team of B.E.E. Certified Energy Auditors and Engineers can help you in saving significant energy. Book a free online session with our experts to learn how you can get started on your energy saving journey.
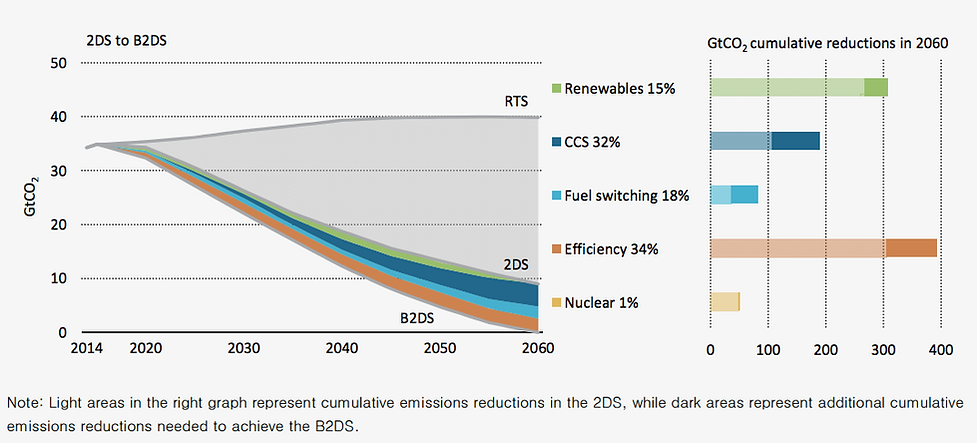
Highlights of our Energy Audit capabilities :
-
Energy Audit team is led by IIT-B alumnus B.E.E. certified & accredited energy auditor with 35+ years of industrial energy audit experience across a variety of manufacturing industries and sectors.
-
Our team consists of Harvard Certified Sustainability expert, B.E.E. Certified Energy Auditors, B.E.E. Certified Energy Managers, Senior Engineers and Junior Engineers with a rich experience and deep knowledge of industrial energy audit services.
-
We cover 360° of energy consumption as part of the audit - i.e. electrical energy, equipment efficiency, utilities such as pumps, compressors, cooling towers, boilers, turbines etc. and also thermal energy through IR thermography. In some cases we also carry out process audit if permitted by the client. In the past we have identified significant energy saving opportunities through process audits as well.
-
All energy saving projects and assignments are closely monitored by the company's founding team through -
-
Daily progress review and reporting
-
Weekly progress review and reporting
-
Timely customer updates and query resolutions
-
-
We adopt a highly systematic approach and divide the entire assignment into 3 phases i.e. Pre-visit, Visit and Post-visit to ensure maximum possible energy saving in your plant.
-
Our focus is on difficult to identify and simple to implement energy saving solutions.
-
All the energy saving recommendations made post the energy audit have an attractive payback ranging from a few months to 12 months. In some cases the payback period could be 18 months or higher.
-
The energy saving recommendations made by us are divided into 3 types:
-
Zero / low investment: Primarily operational and maintenance recommendations or small energy saving retrofits.
-
Medium investment: Some mid-size retrofits or technology upgradation.
-
High investment: Major technology upgradations and / or energy saving project which could be taken up strategically.
-
We believe that energy saving is a journey and not a destination. Owing to our strong commitment to the cause of environment protection we have had the pleasure of saving around 5% to 8% on energy bills for our customers. Have a quick look at our energy audit case-study to understand more about our capabilities and also check out customer testimonials.
You may also like to go through our sample energy audit report of an actual energy audit of a steel plant.
(Aluminum smelter energy audit case-study : Available on request. Drop a mail to info@EnercoEnergySolutions.com or Enerco@Ymail.com)
Any specific query on Energy Audit or Energy Conservation? Get in touch and we would be glad to assist you.
Need more information on energy conservation for your manufacturing facility? Do check out our Videos on Energy Conservation and Energy Audit and the Knowledge Corner page which is frequently updated with interesting content. Energy Audit carried out by our experts can result in significant reduction in your production costs.